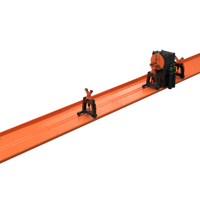
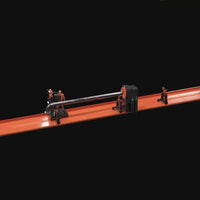
Rotoweld 3.0 Twin Bay
Get the industry's highest productivity output
The Rotoweld 3.0 Twin Bay is all about efficiency and arc-on time. Make loading, unloading, grinding and aligning time losses disappear with the twin bay. Prepare your next spool on the second bay while the Rotoweld is completing a job on the first bay. This is how you'll accomplish up to 300 dia inch in a single 10-hour shift.
- 75mm to 1065mm Diameter Capacity
- 4,535kg Pipe Stand Capacity
- 300+ dia inch Daily Productivity Capacity
Rotoweld 3.0
ROTOWELD 3.0 TWIN BAY
Get the industry’s highest productivity output
The Rotoweld 3.0 Twin Bay is all about efficiency and arc-on time. Make loading, unloading, grinding and aligning time losses disappear with the twin bay. Prepare your next spool on the second bay while the Rotoweld is completing a job on the first bay. This is how you’ll accomplish up to 300 dia inch in a single 10-hour shift.
Rotoweld 3.0
Twin Bay
GMAW, FCAW, MCAW
Welding Torches and Wire Feeder
> Designed with 2 welding torches: one to perform open-root-pass butt welds and the other for filling passes
> Each torch has its own wire spools. Root pass is done in GMAW; choices for fill passes: GMAW, FCAW, MCAW.
> Separate gas shielding system for each torch
> Robotized torch welding arm for fast and repeatable torch positioning on selected pipe diameter
> Torches can be easily switched — optional SAW available.
Robotic Welding Arm
> Self-positioning of the arm in welding position in just a few seconds with no human manipulation
> Welding vision system controls the puddle penetration and adapts welding parameters in real time
> Embedded LED lighting allows the welder to easily align the torch in the bevel before starting to weld.
> Optional fillet weld for slip-on flanges.
Seamless Integration
Proprietary designed rail system
> Rails are the backbone of the Rotoweld 3.0 and can be level on any shop floor conditions
> Rails are factory pre-assembled and pre-aligned for maximum on-site precision
> Seamless integration; no wires lying on the ground
> Welding station and optional fume extractor travel on the rails to desired position simply by using the joystick
> Single Bay comes with 2 rails for a total of 32 ft. (9.75 m).You can upgrade a Single Bay Rotoweld to a Twin Bay.
Heavy-duty Pipe Stands
> 2 pipe stands that can be moved quickly and easily on the rail while staying aligned with the rotator to guarantee perfect positioning
> A hand pump connected to the hydraulic cylinder levels the pipe section easily, efficiently and safely
> Heavy-duty steel idler rolls allow the pipe to turn freely. Optional rubber idler rolls are available for stainless steel application.
> Diameter range: 3 in. to 42 in. / 75 mm to 1,065 mm
> Load capacity: 10,000 lbs. / 4,535 kg
3 in. to 42 in. / 75 mm to 1,065 mm
High-torque Rotators
> Minimal set-up time required due to its self-aligned design
> Specially designed for the Rotoweld to have total control on the weld puddle
> Diameter capacity: 3 in. to 42 in. / 75 mm to 1,065 mm
> Centre line clearance to ground: 65 in. /1,605 mm
> Operation speed range: 0.2 to 1.9 rpm
> Load capacity: 3,000 lbs. / 1, 360 kg
> Maximum torque: 50,000 lbs.-in / 5,649 n-m
> Optional stainless steel grippers
4D Synergy Welding
User Interface Features:
> UI entirely browsable with the Rotoweld pendant
> Large centred image of the torch in the bevel (arc-off) and the weld puddle (arc-on)
> User and Engineering modes easily toggled with the engineering lock key
> Welding program visible at all times with a live cursor that indicates the progression of the weld
> Expandable menus to enter key informationWelding information display.
4D Synergy Welding
Prodatalog™
Gives you:
An overview of your productivity for a period of time that can be filtered by welder, welding programs and job number
A daily report in a chart that contrasts the arc-on-time, the complete procedure and interruption
Details on each joint:
> Displays the welding parameters used for all passes as a function of degrees of rotation
> Displays the complete welding program that was loaded for that joint
> Records a live video of each pass, pushing the limits of investigating welding practices or joint preparation
> Displays the temperature measurements and waiting times between passes for temperature-sensitive material.